Harnessing the power of code optimisation in electronics manufacturing automation
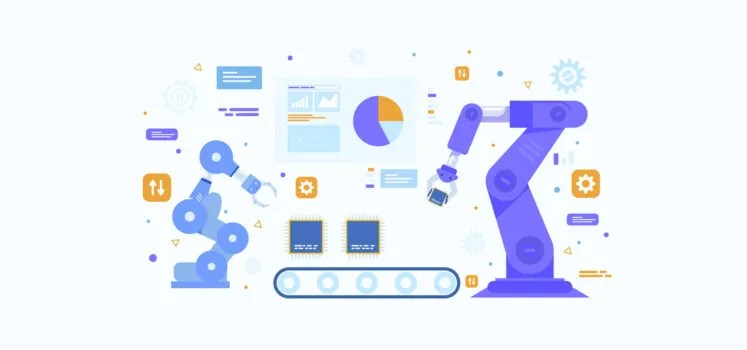
Industry 4.0 is reshaping business and manufacturing processes. Rapidly evolving technologies such as artificial intelligence (AI) and machine learning (ML), cloud computing, and the Internet of Things (IoT) are driving the changes in the electronics manufacturing sector. Adopting these technologies effectively is certain to give businesses a leading edge in the market. However, implementing cutting-edge technologies can be challenging. They often require significant hardware, software, and human resources, and can be extremely costly to implement.
Code optimisation is one approach to reducing the resource demands of implementing automated electronics manufacturing systems. Code optimisation is a unique approach to crafting smarter and more efficient electronics manufacturing automation systems.
In this article, we discuss how code optimisation can revolutionise various aspects of electronic manufacturing.
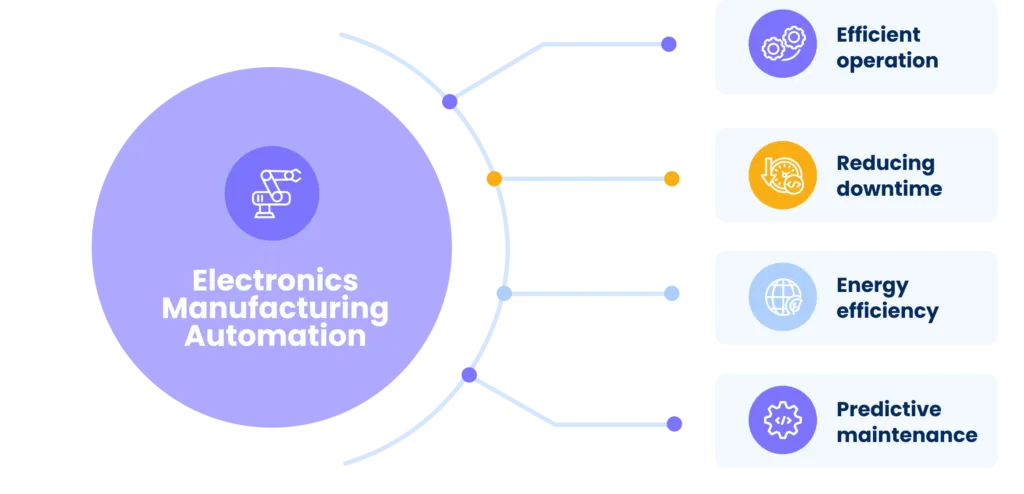
Efficient operation
The primary goal of electronics manufacturing automation is boosting efficiency. Code optimisation can contribute significantly to this goal. By identifying and eliminating redundancies and bottlenecks in code, cycle times may be dramatically reduced, leading to improved response times in automation systems. By streamlining code and reducing inefficiencies that cause lags in production, companies can achieve higher overall operational efficiency and throughput.
Reducing downtime
Machine downtime is one of the most considerable challenges in electronics manufacturing. It hampers productivity and can lead to substantial financial losses. Implementing optimised code is an effective strategy for countering this challenge. As code optimisation allows automation processes to function more smoothly, it leads to a consequent reduction in machine downtime. The increase in uptime allows for higher overall productivity and reduces potential losses associated with system failures. All in all, streamlined and optimised code can immensely contribute to a more resilient, continuous, and profitable production process.
Energy efficiency
The benefits of code optimisation are not only limited to operational efficiency. Code optimisation can contribute significantly to making automation systems energy-efficient. Optimised code reduces the energy demands of various components in an automation system and consequently, leads to less power consumption. Given the scale of electronics manufacturing systems, even minor efficiency gains can lead to a significant reduction in the energy consumption of automation systems. Especially considering the emphasis placed on sustainability, enhancing energy efficiency via code optimisation is not merely a financial advantage but also an environmental responsibility.
Predictive maintenance
Code optimisation is also paving the way for predictive maintenance strategies in electronics manufacturing. By efficiently gathering and analysing data from automation systems, optimised code can help predict potential system failures before they occur. This proactive approach reduces downtime, cuts unplanned maintenance costs, and enhances overall operational reliability. The ability to adopt a predictive approach to maintenance will enable businesses to stay ahead of the competition.
Code optimisation is a powerful strategy with far-reaching benefits for electronics manufacturing. It fosters efficient operation, reduces downtime, promotes energy efficiency, and facilitates predictive maintenance. As the world continues to ride the wave of digitalisation and automation, investing time and resources into code optimisation can undoubtedly lead to more efficient, resilient, and sustainable automation systems.
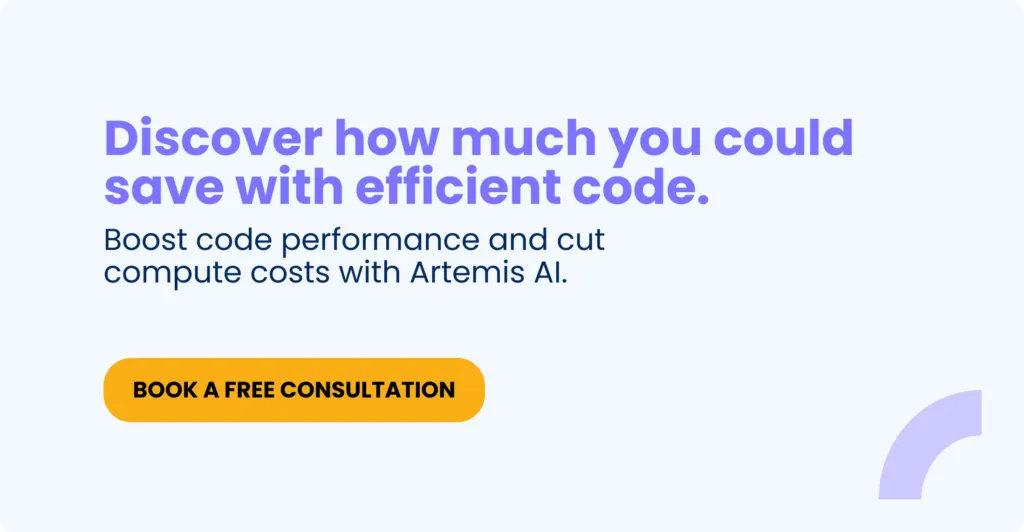